Search
Repairing a pressure vessel
Client : A mining company with activities in Northern Quebec
An onsite project
Sometimes, the equipment to be fixed can’t be brought into our shop. Like in this case: a pressure vessel needed repair, but was located in a mine hundreds of kilometers north of our facilities! Sending it by plane or road was not an option, so the work had to be done onsite, with all the preparation that entailed.
Expecting the unexpected
Right from the start, FAB 3R knew the project had to be planned out—right down to the smallest detail—because the repair work had to be done during a scheduled shutdown of the mine. Since production shutdown is extremely costly in mining, the repairs absolutely had to be done without the slightest delay. In other words? FAB 3R had less than a week to get the tank back in working order. Our team prepared the work very carefully to be sure that once mine production was stopped, everything would be in place for us to do the repair as quickly as possible.
Before beginning the work, FAB 3R had to perfectly understand the job ahead, decide on the best approach and select the right tools. We started by flying up to inspect the tank during a site visit. To save time, a subassembly was made in our facilities and sent to the mine by plane. This way, all we had to do during the shutdown was install it!
Since the repair was being done on a pressurized tank, FAB 3R also had to coordinate with Régie du bâtiment du Québec visits. These building authority inspectors confirmed—every time!—that our work met ASME/R-STAMP certification requirements.
From a technical standpoint, the project brought its own batch of difficulties. Since the products used inside the tank are very corrosive, the metalwork had to meet very specific criterias. The material used in this case, Hastelloy G30, is a special anti-corrosive, high-resistance metal requiring very particular welding skills. Also, this type of metalwork requires not just the right filling metal, but above all, the right welding procedures. Our ASME-certified welders had all the qualifications needed to do this delicate welding job in compliance with the standards.
On schedule and up to standards
Given the tight schedule, two welding teams, each backed by a supervisor, tag-teamed to work continuously through the week the mine was shut down. They got the repair done on time and in compliance with the building authority’s standards. A true success story!
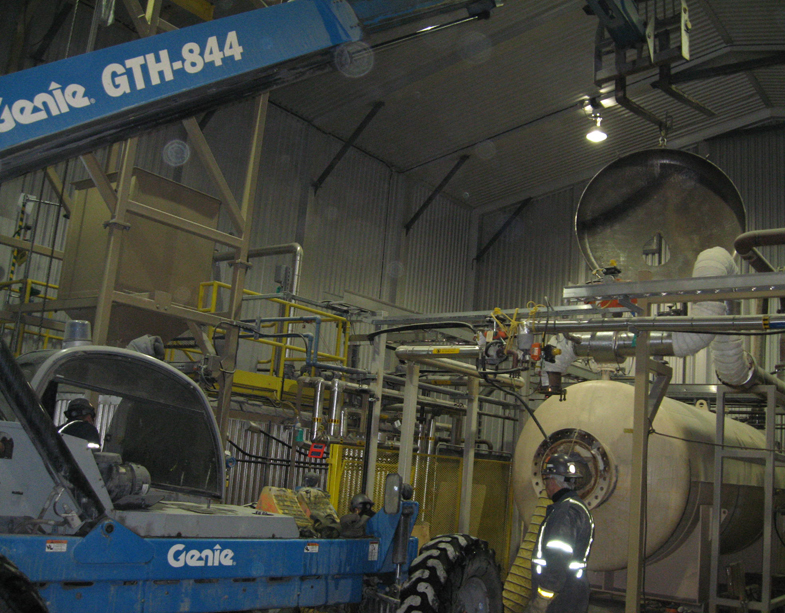
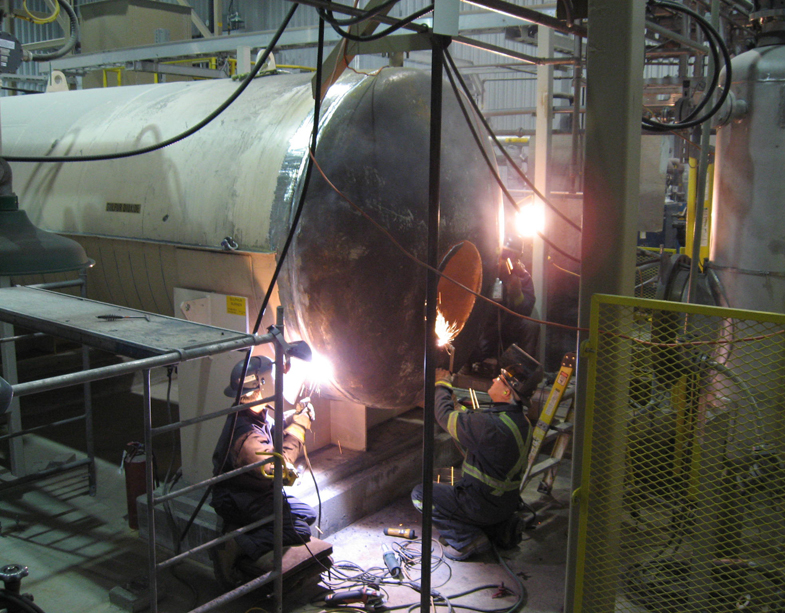