Search
Precision machining
Client : A well-known OEM in the hydro-electric energy industry
Giant parts to machine
Our client had to implement three new generating unit groups and needed three new turbine shafts. Given the required dimensions, they couldn’t turn to just any company: they had to find one who could not only machine the nearly 9-meter-long shafts but do so with exceptional precision to meet the required tolerances and surface finish.
With its experience machining large-scale equipment, FAB 3R was highly qualified to successfully deliver this project.
And what’s more, one of North America’s two largest horizontal machining lathes can be found in its facilities!
Big dimensions, big expectations
When we say FAB 3R is up for huge projects, we mean exactly this kind of project: machining a turbine shaft that’s 2.4 meters in diameter, 8.8 meters in length and 91,000 kilos in its raw state! In fact, these shafts are so big they currently hold our record for the largest parts we’ve ever machined on our horizontal lathes. (Incidentally though, our lathes can actually do bigger—we’re just waiting to set a new record!) Despite the parts’ humongous size, the tolerances and surface finish had to be very fine.
In large-scale machining, the slightest error can be costly. Very costly. This is why FAB 3R put all its manufacturing expertise to work to fully understand the client’s plans, estimates and engineering instructions before plotting out the various steps of machining. We then created the shaft’s various sections progressively—this was key to ensuring the dimensions perfectly met the specs.
Like for all hydro-electric projects, quality assurance is essential. There are many standards to be met and loads of documentation to submit to regulatory bodies. Throughout the machining and finishing, FAB 3R’s inspection team had to file all the required reports to prove the compliance of all the parts, and the validity of our measurements and measurement methods.
Equipment and expertise make all the difference
Thanks to the unequaled precision of its LINÉ lathe, FAB 3R machined these parts on deadline, complying with our client’s very strict tolerances and creating a surface finish between 0.2 (N4) and 0.8 (N6) micrometers (8–32 R.M.S).
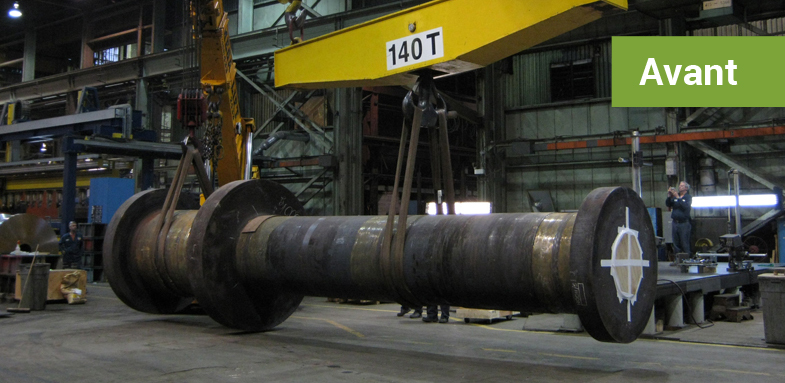
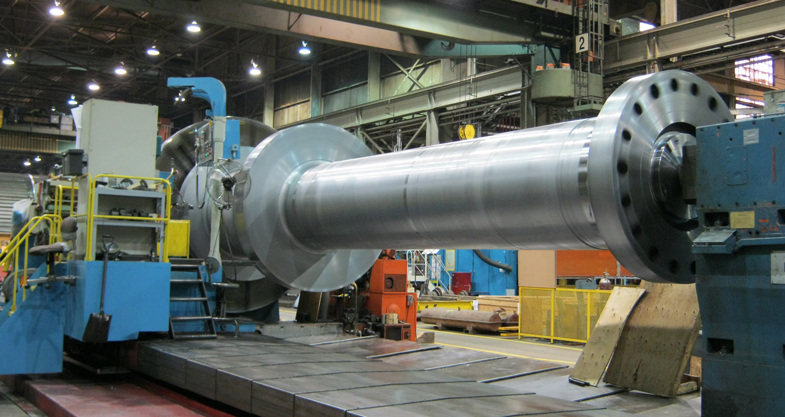
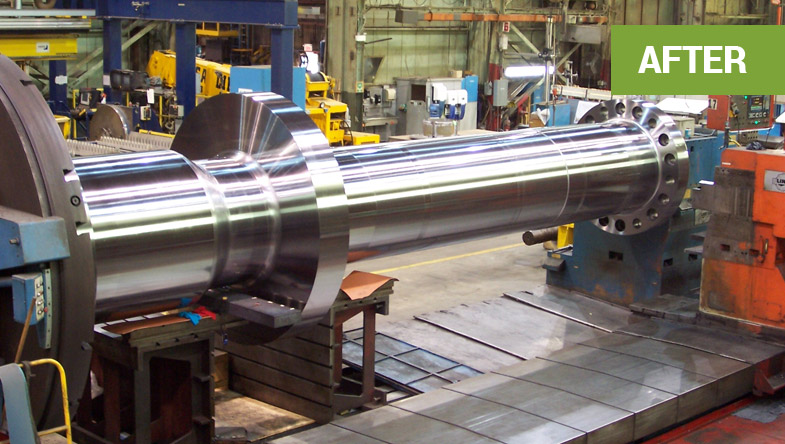