Que cherchez-vous?
X
Aucun résultat
Recherche en cours ....
Entrez au moins {{MinCars}} caractères
{{result.Name}}
{{result.SubInfo}}
Quelques réalisations
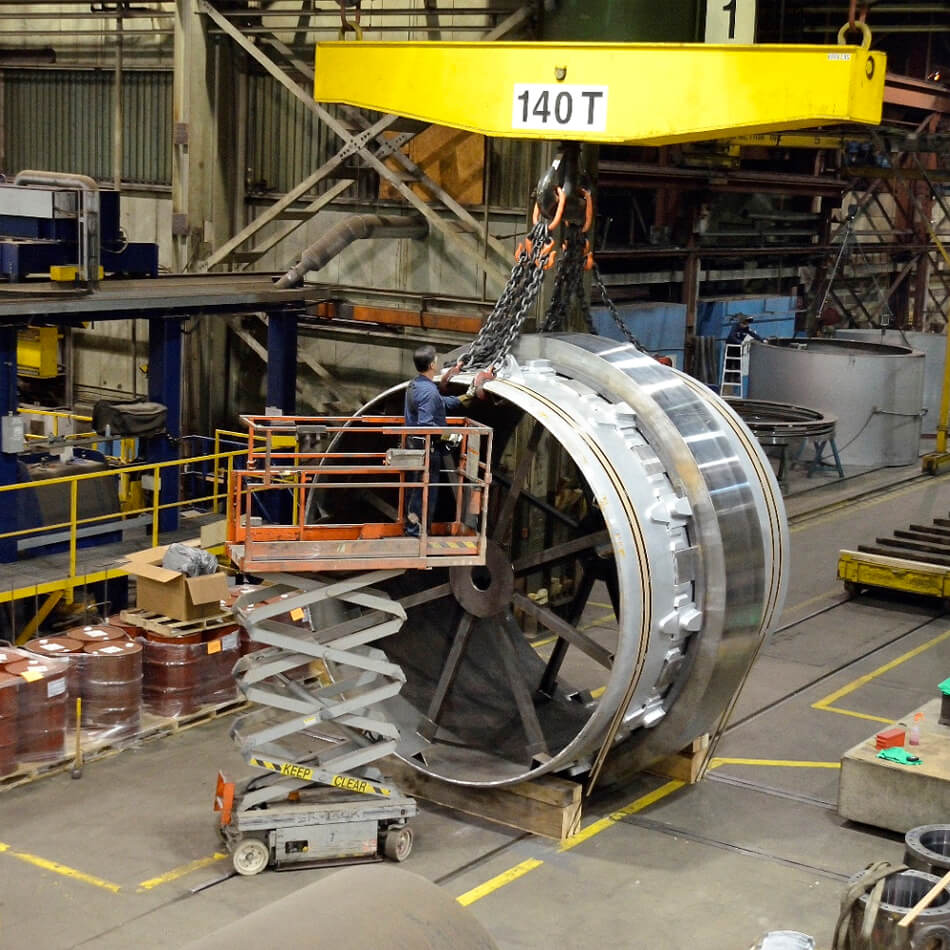
Fabrication et usinage de composantes de four industriel
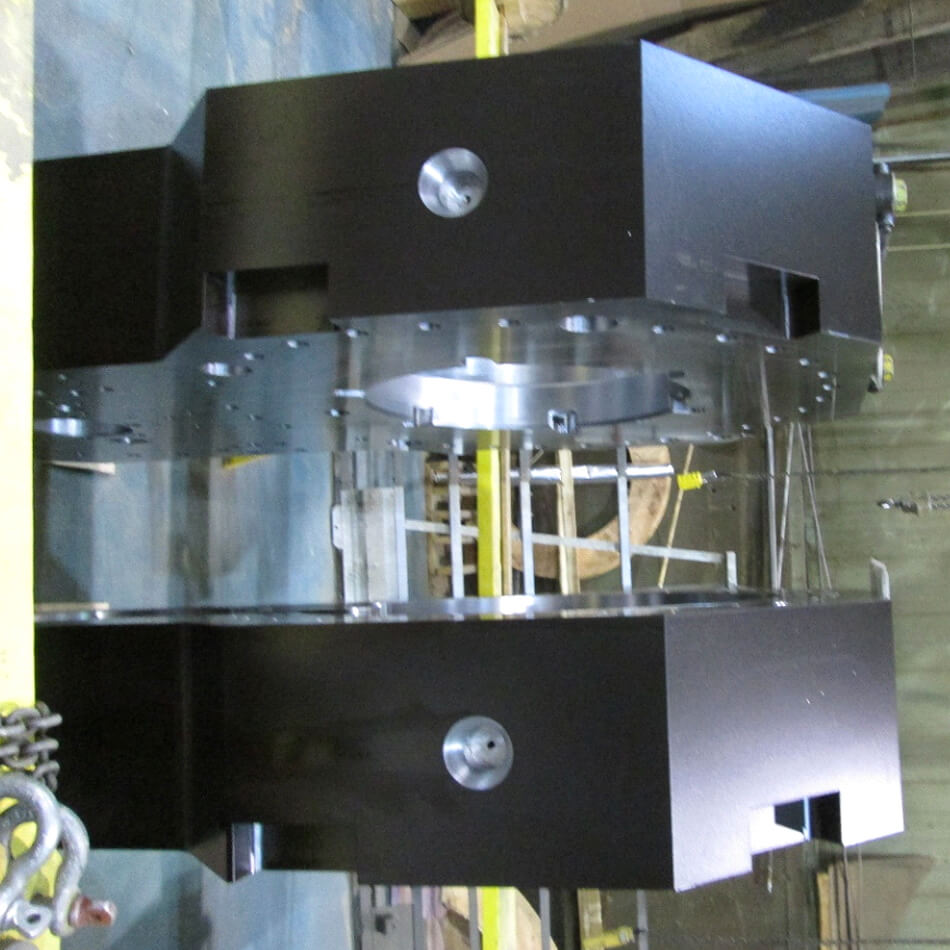
Usinage de composantes hydrauliques pour secteur automobile
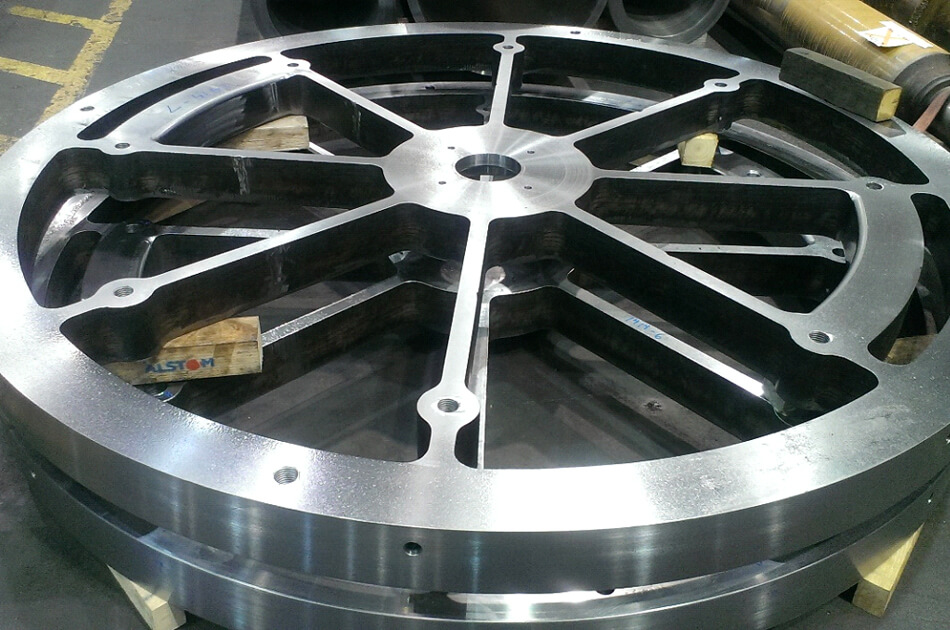
Usinage haute précision d’outillage pour moule de pièces aéronautiques
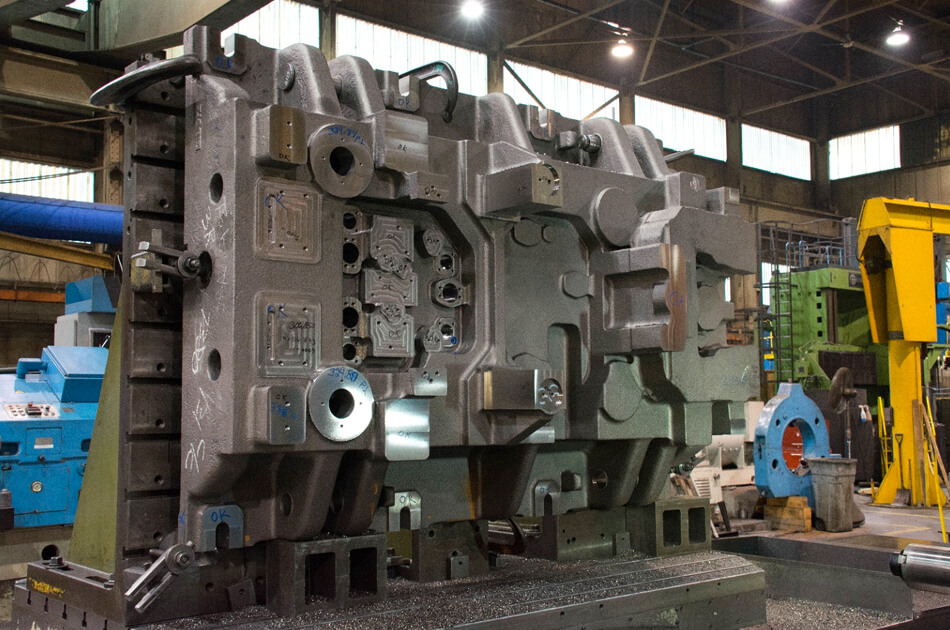
Usinage haute précision pour outillage du secteur automobile
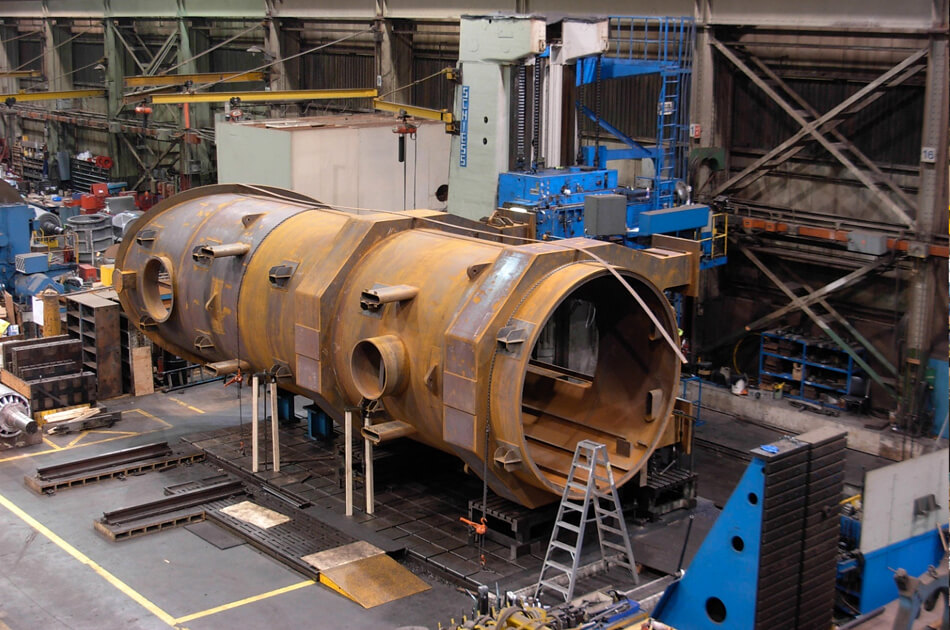
Usinage d’outillage, grand format, pour banc d’essai du secteur aéronautique
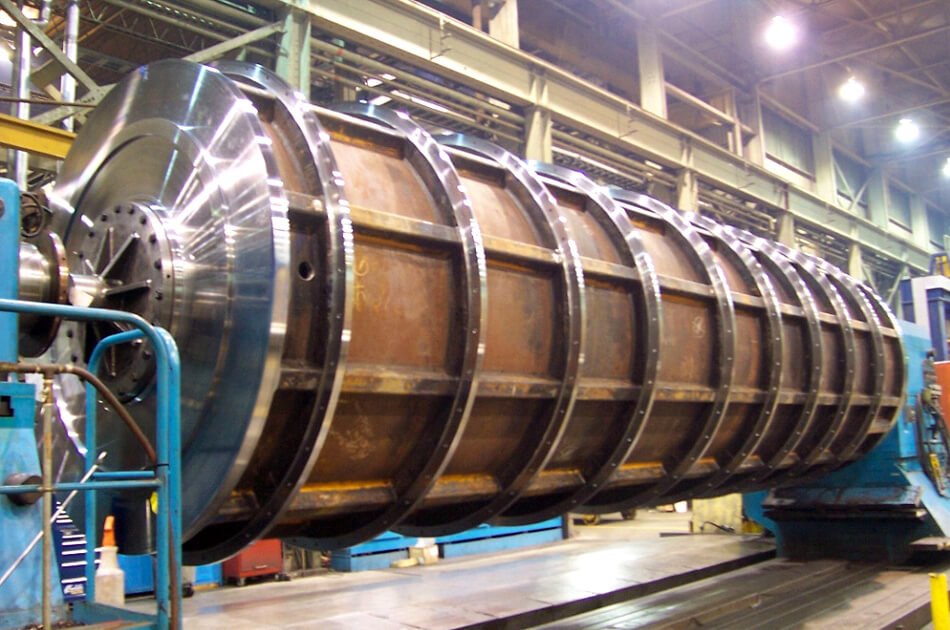
Fabrication et usinage d’outillage du secteur tréfilerie